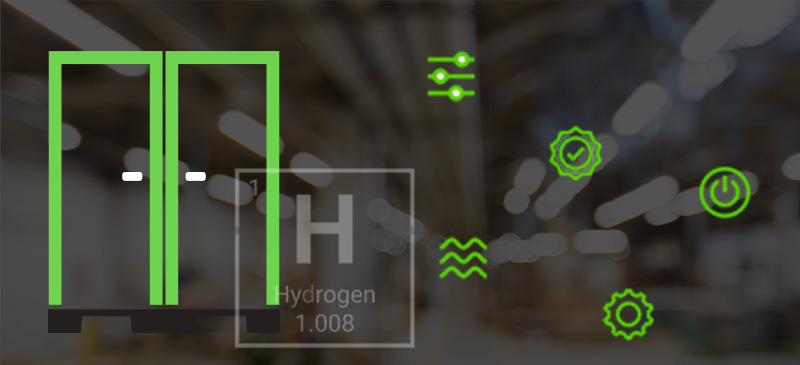
Effectively Enabling Hydrogen Purification for Process Equipment
Hydrogen is used in many processes across the semiconductor industry, like annealing, epitaxial growth, lithography, and as a carrier gas for hydride dopants. Hydrogen gas usage is only increasing, and along with that comes constraints on supply chains and markets. Hydrogen generation is also becoming more prevalent in order to mitigate traditional supply chain issue, like trucking, plant shut downs, and more.
It is crucial to utilize the right kind of gas purifier when working with hydrogen, and to find the right partner that enables you to do so successfully. ARM Purification is focused on offering gas purification solutions for complex and myriad application and is the trusted source of high and ultra high purity gas purifiers and equipment, as it delivers point-of-use and bulk gas purifiers to customers around the world.
ARM Purification recently introduced the redesigned APS60 series of purifiers, including the APS60-CXXX series of hydrogen purifiers (XXX is the flow in Nm3/hr). For any process, ARM Purification is equipped to handle hydrogen purification; traditionally utilizing H2 from liquid, tube trailers, and other sources and purifying it to 8N or 9N outlet quality.
This blog post will explore challenges with traditional purification technologies, safety considerations of hydrogen systems, and ways to solve complex gas purification challenges.
Challenges with Traditional Heated Media-Based Purification Technology
While bulk purifiers have traditionally been utilized on systems providing fairly constant flow requirements, ARM Purification has introduced the ability to provide purified UHP 9N Hydrogen gas in a process environment that demands high flow rate variations and fast response times for the success of the process. These systems are sized up to 300 Nm3/Hr and are fully PLC controlled with hydrogen safety features built into the unit.
Using traditional heated media-based purification technology for hydrogen purification is somewhat difficult in applications that require high flow rate variations, such as EPI, due to the construct of the material’s reaction towards hydrogen. The traditional purification media, which is often a metal getter, reacts with hydrogen in a reversible manner, giving the ability to increase purifier vessel pressures and temperatures very quickly upon flow demand through the unit. This is due to the fact that the hydrogen can react exothermically with the media, and constitutes a reversible reaction in the media that is both temperature and pressure dependent.
Unlike oxygenated species and hydrocarbons, which are chemically bonded to the material upon reaction, the hydrogen goes into solid solution and is a reversible reaction. Therefore, under high flow requirements, the temperature increase needed to optimize purification efficiency must be monitored real time, along with the pressure, in order to control the potential for increases in both, without the pressure loss associated with membrane H2 purifier technology.
Stringent Safety Considerations of Hydrogen Systems
The safety considerations of hydrogen systems are stringent—but with a solution like ARM’s updated APS60 platform of purifiers, there exists the ability to automatically purge the purifier system with Argon gas, and provide for a safe system shut down in case of emergency. This shut down is then followed by an automatic process to re-introduce H2 into the media, thus providing a hydrogen compatible media to resume the purification of the hydrogen gas quickly and safely. All of these processes are PLC controlled and have been fine tuned based on system user input and design engineering parameters, include HAZOPS analysis and best practices followed from AES’ SEMI-GAS line of gas cabinet equipment, and SEMI guidelines. Some of the safety features considered standard are exhausted cabinets, Z-purge electronics, hydrogen gas sensors, and safety interlocks all designed for safe and efficient operation.
The challenges of taking a heated, getter style hydrogen purifier from idle to full process flow conditions have been met by a combination of tight process controls which allow for temperature and flow changes quickly and effectively, and the possibility of user adjustment through the HMI within the process parameters set forth at the factory.
Discover Solutions for Complex Purification Challenges
ARM Purification delivers solutions for the semiconductor industry’s various challenges. ARM has now included Ethernet as a standard offering, and users now have the opportunity to provide UHP H2 and real time monitoring for process hydrogen in variable flow rates for processes that require it in the most demanding of semiconductor processes. The purifier system can be tied in to SCADA or process control systems for full visibility, and comes with standard with sub-micron particle filtration, and the availability of industry leading 1.5 nm filtration.
ARM Purification now has the product which excels under delivery system constraints like flow variations or high pressure loss of membrane purification technology. Learn more by visiting www.armpurification.com.
Share this Post: