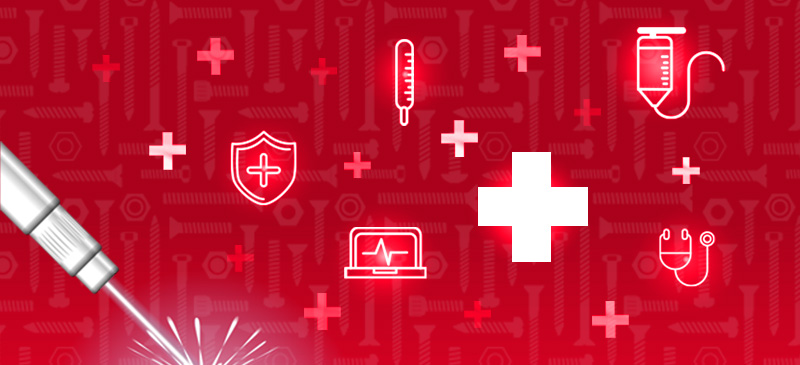
Identifying the Right Welding Technology for Medical Devices
The importance of medical devices and their proper use on patients cannot be understated today. And with ever-evolving technology comes new medical innovations, like wearable devices. These smart watches, sensors, and monitors can be placed on or inside the skin, making it imperative that the technology is flexible, durable, and safe. Along with these new innovations, legacy medical instruments like spinal implants and orthopedic screws must also be produced with an eye for detail and adherence to strict standards.
Engineers are tasked with developing these medical devices and ensuring they meet the highest levels of exhaustive safety regulations. Any imperfection can mean life or death to a patient. The relationship between a medical device and a patient is critical, so every tiny piece must be precisely constructed.
The quality of a medical device is subject to various factors, like its materials and design, as well as the reliability of its manufacturing process and the costs associated with its creation. Manufacturers must be able to produce consistent quality at the most time- and cost-effective rates in order to not only ensure patient safety, but to benefit the company bottom line as well.
Therefore, the right welding application must be used for the unique devices whose parts require welding. For example, under-the-skin devices like replacement heart valves or neurological implants have the highest criteria, and must receive the FDA’s Class III designation, meaning they are determined to be high-risk as part of the CE marking process. For both Class III device manufacturing and the development of other wearables like monitors, incorporating the right welding and bonding technology is crucial. This blog post explores different kinds of welding technologies for medical devices.
- Laser Welding
Laser welding is ideal for ensuring automated precision in small and intricate welding applications because of its small and precise beam. Nd:YAG welding systems are the most common, as the 1,064 nanometer wavelength is a good wavelength for coupling to stainless steel and titanium (they do not work on copper). Laser welding systems are effective at welding certain parts of bone screws and spinal implants, as well as types of stents, drug pumps, implantable valves, and other life-supporting devices. It provides at least an even greater accuracy to legacy processes, and offers some key advantages to manufacturers. Laser welding requires no vacuum chamber, as it can be done in an inert gas atmosphere, generally nitrogen or argon based. Laser welding is usually more flexible and much quicker. It offers features like vision systems, which use cameras to recognize parts, identify weld areas, and locate the exact position for the laser to begin working. This dramatically improves yields and other weld acceptance criteria. Many medical device manufacturers now opt for automated laser welding as a way of reducing costs and dramatically improving welding process control.
- Glovebox Welding
Glovebox welding works well for specialized applications that require a high purity inert atmosphere for such applications as filling a device with an inert gas and then sealing it or when exterior shielding with an inert gas is difficult. A glovebox—also called an atmospheric enclosure or an inert gas enclosure—is a sealed work area that has built-in glove ports, pass-through chambers, and interlocking doors to allow the handling of objects inside a controlled working environment. Typical applications include the hermetic sealing of electronic and medical components that require a high purity, moisture-free inert atmosphere like Argon, Nitrogen, or Helium. The benefits of glovebox welding include the ability to control the moisture and oxygen content to ensure that the strength and quality of the weld complies with standards. The glovebox confines the area away from the air and prevents the propagation of protective gases, and makes it easier to weld more difficult-to-access places or extremely thin surfaces.
- Laser Marking
Laser marking is etching and engraving with high standards of precision and accuracy. It’s a permanent process that uses a beam of concentrated light to create a mark on a surface, and is typically performed with a fiber, pulsed, continuous wave, green, or UV laser machine. Medical instruments undergo different types of laser marking based on their purpose. For example, metal medical tools require traceability markings to ensure their sterilization process and usage requirements are strictly adhered to. Laser marking offers benefits like greater operational efficiency and productivity, less waste and downtime, minimized threats like quality and counterfeiting issues, and ensured compliance with industry regulations.
- Metallurgical Analysis
Metallurgical Analysis is the rigorous testing and inspection of weld quality. While this process can reveal the condition and makeup of materials with macro, micro, and scanning electron microscope examinations it is typically used to confirm the weld nugget size and geometry. Measurements are taken and then statistical process techniques are employed to determine the robustness of the weld process. These analyses show the microstructure, manufacturing processes used, and specification adherence. The benefits of metallurgical analysis lie in its ability to thoroughly assess defects, determine structural features, identify alloys, evaluate heat treating effects, and ensure that materials characteristics align with their specifications.
Meeting the Highest Standards
The medical field has strict regulations and standards, and for a good reason. Patient safety is of the highest importance, and their safety starts from the very beginning of the supply chain, with the components that make up medical devices.
According to the International Organization for Standardization, regulatory requirements have become more stringent than ever throughout every step of a medical product’s lifecycle. Organizations in the medical industry are expected to demonstrate their quality management processes and ensure best practices in order to meet today’s safety and reliability demands. ISO 13485 is an internationally agreed standard that sets out the requirements for a quality management system specific to the medical devices industry.
This standard is designed to be used by organizations involved in the design, production, installation and servicing of medical devices and related services. And it’s essential to ensure that the organization performing delicate and precise welds within the medical industry is ISO 13485 certified.
Choosing the Right Partner for Medical Welding
In medical applications, the quality of welded components directly impacts patient quality of life. It’s thus important to choose the right partner for medical device welding. As a company experienced in meeting the critical compliance-driven requirements of the medical sector, Apex Precision provides outstanding purpose-driven medical welding services, including laser welding, marking, and metallurgical analysis, engineered with an acute understanding of your smallest and most complex welding needs.
Apex Precision is ISO 13485 certified and understands how precision impacts outcomes. From medical implants to precision-engineered instruments, medical prototypes and surgical devices, we deliver a full range of welded components with repeatable and reliable precision.
Learn more about Apex Precision’s purpose-driven precision welding services exceeds expectations for repeatable quality, accuracy, and reliability.
Share this Post: