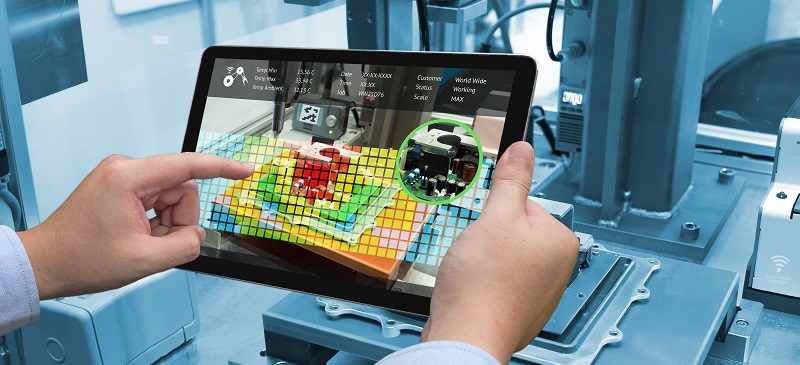
How Industry 4.0 is Making Semiconductor Fabs Even Smarter
If you’re in the manufacturing space, you’ve probably heard rumblings about Industry 4.0: what is being seen as the next industrial revolution that will reshape manufacturing through digitization and the creation of “smart factories”. While the first three manufacturing disruptions centered on the use of steam power, then electricity, and then the introduction of computers into the workplace, this fourth revolution is all about leveraging automation and data exchange to drive new production efficiencies.
But what does this really mean for companies that are already implementing highly advanced and sophisticated manufacturing techniques, like those in the semiconductor industry?
According to recent findings by McKinsey, semiconductor fabs that have established disciplined lean manufacturing programs can realize additional labor productivity gains of 30 to 50%, and maintenance productivity gains of 10 to 20% by introducing Industry 4.0 techniques. Here are some of them:
Reducing Operator Touch Time with Automation
In back-end semiconductor factories, the amount of time an employee spends handling material or operating a machine represents 30 to 50% of all labor. Optimizing worker-machine ratios against capacity through lean initiatives can incrementally improve labor productivity, but Industry 4.0 tools can help accelerate these gains through smart automation. For example, a gas delivery system that performs purging and cylinder switchover automatically can do so when needed, in real time, without human intervention, greatly improving process efficiency while allowing operators to focus on higher value, bottom line-driving tasks.
Seeing Operations Clearly with Virtual and Augmented Reality
Front-end semiconductor fabs, particularly when it comes to wafer fabrication, already use highly automated processes – meaning that there are fewer operators to oversee massive amounts of equipment and operations. This is why virtual reality (VR) and augmented reality (AR), new innovations that are part of Industry 4.0, can help give these operators greater visualization into, and control over, their sprawling production environments. What if they could simply face their mobile device or tablet to a piece of equipment and instantly see real-time data on its status? Even the ability to visualize the entire production floor in real-time using VR 3D maps seems to be a not-so-distant possibility thanks to Industry 4.0.
Capturing Machine Data for Continuous Optimization
Another way that semiconductor fabs can leverage Industry 4.0 is by equipping their machines with sensors that monitor system performance, and that deliver that data to operators to enable ongoing optimization. Teams can analyze the insights gathered and adjust process parameters as needed – in real time – to monitor status and instantly adjust performance, predict maintenance requirements to preempt failures, remotely steer machine processes, and much more. For example, data collected by a gas cabinet through continuous system monitoring and alarm logging can be used in correlating spikes or losses in a fab’s overall yield, helping to identify the particular production step responsible so that it can be further optimized or addressed.
While it is true that the semiconductor industry is among the most advanced in manufacturing and data collection already, most fabs are still only using a fraction of the information they acquire today to their benefit. Those that embrace emerging Industry 4.0 tools early will be able to better harness the power of this data to create new insights and build efficiencies, and in turn drive new levels of productivity, throughput, and quality.
Share this Post: