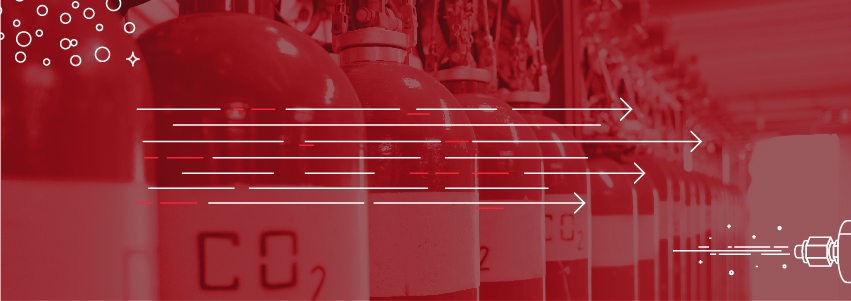
The Properties of Gas Purity: Physical Gas Separation
Gas purity is critical for a diverse array of applications and industries, ranging from semiconductor and electronics, to clean energy and solar, industrial manufacturing, and universities and research labs. Over the next few weeks, we’ll be releasing a series of blog posts focused on three key aspects of gas purification. In this, the first issue of the series, we’ll cover the basics of physical gas separation and the three core technologies used.
Ensuring that process gases uphold highly stringent purity levels is not only integral to maintain consistency and integrity throughout production, but also to protect the wellbeing of operators working with these gases. In order to achieve exacting standards, operators must employ different methods of gas purification, contingent upon gas type and specific requirement.
One approach to purification is physical gas separation, which involves the separation of one component from another (e.g., hydrogen from natural gas). Let’s examine three primary technologies used for physical separation, each varying in degree of purity achieved:
Membrane Separation
Membrane separation technology is commonly used when industrial gases do not require stringent purity standards to be upheld. With this technology, thousands of hollow fiber membranes are fitted into a housing where compressed air is fed through one side. Different gases have different diffusion rates on the fiber wall, and so varying flow rates can be used to vent out contaminates that move through the systems while preserving the desired gas.
For industrial gases, membrane separation—preferred for its lack of moving parts—is often enough to achieve the desired level of gas purity. For high and ultra high purity gas applications, however, where purity levels of greater than 99.99% must be achieved consistently, other systems must be utilized.
Pressure-Swing Adsorption
When gases must be purified to the high parts per million (PPM) level, pressure-swing adsorption (PSA) is utilized. This technology leverages pairs or series of vessels that are packed with adsorption media like carbon molecular sieves, zeolites, and charcoal, which are then pressurized to over 100 psig. Van der Waals forces –relatively weak electronic forces that attract neutral molecules to one another in gases and most organic liquids and solids—cause the feed gas stream to be physically adsorbed on the media. The desired gas, which is adsorbed at a different pressure and temperature than the impurities, then passes through with impurities removed. Since impurities are adsorbed into the media when PSA is used, vessels must be regenerated, which can be done by venting the atmospheric pressure, thus releasing the trapped impurities, and then repressurizing the vessel. Without this process, impurities remain, contaminating the next batch of gas.
A key advantage of pressure swing style purification is the level of purity it is able to achieve, providing up to 5Ns pure gas. As a result, it is suited to a diverse range of applications with more rigorous gas purity requirements than can be met by membrane style separation, such as pharmaceuticals, laboratory research, aerospace, and certain electronics applications.
Cryogenic Distillation
For the most stringent purity requirements, cryogenic distillation should be used. Removing impurities to a low PPM level, cryogenic distillation uses gases’ unique boiling points for separation. First the gas is chilled and passes through a sieve to remove trace impurities like moisture, then it is fed into a distillation column where it is cooled to cryogenic temperatures against outflowing gases. Due to differing boiling temperatures, air travels up the column through a series of trays, and cascades down as reflux liquid. During this continuous process, impurities are removed.
Cryogenic distillation is the preferred technology for applications with ultra high purity requirements in which a single lapse in purity can be detrimental to safety or operational outcomes. It is important to note that the size of the cryogenic distillation system varies greatly depending on the application and amount of pure gas being used.
The Purification Technology for Every Purification Standard
The ideal physical gas separation approach is highly dependent on the gas to be purified, the application, size of operation, industry, and more. No matter your exact purification requirements, ARM Purification has the point-of-use, micro-bulk, or bulk purifiers needed to keep your gas free of trace impurities and ready to enable your mission-critical processes. Tell our team of purification experts a bit about your purification requirements and we will connect you to the best-fit solution.
Share this Post: