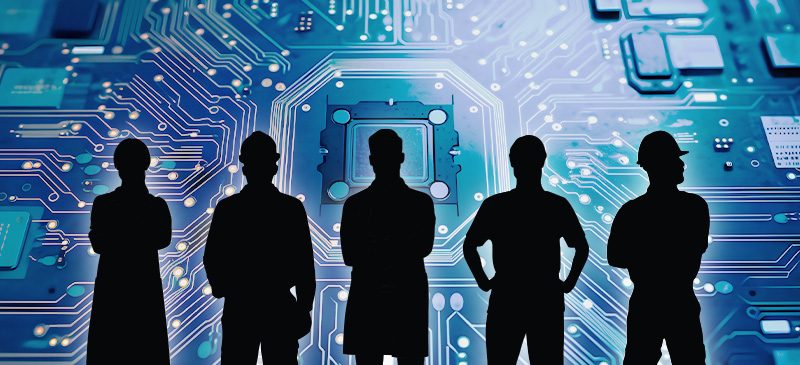
Disappearing Talent: Top 3 Takeaways from the Semiconductor Skills Shortage
It’s no secret that the semiconductor industry has experienced a series of supply chain shortages and slowdowns that have had a tremendous impact on chip manufacturing. It has given way to a new, critical issue that fabs are currently experiencing—a skills shortage.
It’s crucial that organizations recognize the magnitude of the skills shortage and its effect on the industry, and take action to mitigate the issue. This blog post will focus on the top three challenges the industry is facing due to the lack of the right personnel in the right roles within the semiconductor sector, and uncover how the US is working to overcome shortage-related obstacles.
The Origin of the Skills Shortage
The COVID-19 pandemic triggered a resigning spree in the U.S., with 128.3 million workers leaving their roles between early 2021 and August 2023. Currently, the U.S. has about 9 million job openings but only about 6.5 unemployed people.
The semiconductor sector, which is among the many industries with a significant number of current job openings, is in a particularly difficult position. Industry positions require a diverse skill-set and robust knowledge in the field, making semiconductor manufacturers take twice as long to hire the proper personnel compared to other industries. The hiring bottleneck is as significant as it is difficult to overcome, but there are far more factors to consider when unpacking the semiconductor skills shortage.
Today, the tech industry is facing a significant shortage with an estimated 3.85 million jobs in technical fields to be created by the end of 2030, but only 2.45 million will possibly be filled. This leaves a 1.4 million jobs gap. Deloitte predicts over 100,000 technical workers will need to join the industry every year to fill this gap—however, there are less than 100,000 graduates with required degrees each year. Among the 3.85 million tech jobs added by the end of 2030, 115,000 of those are specific to the semiconductor industry, but an estimated 67,000 of them will remain unfilled.
The Top 3 Takeaways from the Skills Shortage
The skills shortage is a complex issue with a multitude of variables affecting it. The top three reasons it continues to be a pressing issue, however, include:
- A Large Education Gap and Poor Knowledge Transfer
With many experienced workers retiring, the semiconductor industry is tirelessly trying to replace them with the next generation of workers. Unfortunately, there aren’t enough students to fill these roles, and the older generation may not be able to transfer their knowledge efficiently to younger employees.
After the pandemic, the resulting recession and inflation caused training programs and other semiconductor education courses to increase significantly in price. In order to work in the field, students are required to pass difficult courses in the math and science disciplines, such as engineering and physics. These courses are known for their rigor, making students fear the risk of failure and wasting money, thus choosing not to enroll in these programs in the first place.
Rochester Institute of Technology, an institution known for its engineering programs, is struggling to enroll undergraduates in its microelectronic engineering program, with an average of only 20 new students a year. Compared to the 200+ students in its mechanical engineering program, the semiconductor-related program is a stark contrast. Coupled with the struggle of attracting students to choose its programs, semiconductors are competing with larger firms for engineers. Without enough candidates with the necessary expertise, the industry is at risk of facing a shortage of about 70,000-90,000 workers over the next few years.
- Tech Advancements that Require Specialized Skills
The semiconductor industry has a lengthy number of different positions that must be filled in order to maintain efficient operations, each requiring its own subset of skills. Some of these positions include electricians, pipefitters, welders, electrical engineers, operators, technicians, and designers. Each job is as important as the last to keep the semiconductor supply chain moving.
The rise of new technological advancements, however, is affecting various operations within the semiconductor industry. With the introduction of artificial intelligence (AI), automation, machine learning, and digitization, the skills required for semiconductor positions seem to be ever-evolving—so manufacturers must ensure they are considering the savviest candidates with up-to-date skill sets.
Coupled with emerging technology, there is a high demand for specific expertise to operate these tools and software systems. Employees must keep up with the seemingly endless technological changes, updating their skills and expertise to fit what is demanded by the industry. This introduces a potentially large problem: a significant gap between the skills the workforce has and the skills the industry requires.
- Potential Engineers Leaving the U.S.
Skill shortages affect many different professions, but those in semiconductor engineering require a robust knowledge of statistics, physics, and electrical engineering. With so few students in semiconductor-related programs and willing to take on such advanced courses, it’s important for the industry that new graduates begin working at one of the country’s semiconductor facilities post-graduation. However, this isn’t happening. About 16,000 Master’s- and Ph.D.-level international engineers end up leaving the U.S. each year, and by 2030, the semiconductor industry is projected to lose a total of 17,000 of these new engineers.
These numbers reflect a large percentage of America’s engineering students. Over 50% of Master’s and over 60% of Ph.D. egineering graduates. at U.S. colleges and universities are foreign citizens. Among those, 80% of Master’s graduates and 25% of Ph.D. STEM foreign graduates do not stay in the U.S. post-graduation.
This opens the door for recruiting challenges for smaller hubs in the U.S. as well as retaining talent from the unfilled training and graduate programs the country currently has.
How the U.S. is Responding
The semiconductor industry requires employees with very specialized knowledge and who also come from comprehensive training programs. However, there has been an insufficient number of training programs, limiting the pool of qualified candidates. To combat the projected increasing gap, companies are partnering with academic institutions to provide semiconductor-related training programs. Some of these training programs across the U.S. include:
- Micron’s new workforce program – Chip camps for middle and high school students
- Arizona Community College’s 10-day program – A program that helps students become entry-level technicians
- Hillsboro Oregon School District’s two-year advanced manufacturing apprenticeship program – A program for 16- to 18-year-old students to receive credit for working on manufacturing floors
- Purdue University’s online course – A partnership with a few other institutions that provides a free online course titled “Semiconductor Fabrication 101”
Industry leaders are also taking part in the education reform, with the creation of the Semiconductor Education Alliance. Their goal is to create more educational and training opportunities to fill the job gap and inform the next generation of skilled semiconductor engineers.
Since their initiatives began, there has been an 80% increase in full-time entry-level semiconductor job applications and a 40% increase in internship positions. However, retaining foreign graduates remains a struggle as immigration policies are complex, but companies are working to make amendments. Some of these potential changes include raising visa caps and approving more H-1B visas to improve the retention of foreign engineers.
The Biden administration is also creating five workforce hubs to train people of color, women, and other minorities in the STEM fields. Finally, the CHIPS and Science Act has introduced over 50 new facility projects and over $210 billion in investments, which is predicted to lead to growth in this area
A Partnership in Navigating Skill Shortages and Other Complex Industry Matters
The semiconductor industry is an ever-evolving landscape, with continuous innovations and changes that require precise navigation and understanding. Applied Energy Systems is the industry expert with thorough knowledge of not only the complexities of the sector, but in implementing gas delivery and purification solutions that can help your organization remain equipped with the right equipment and able to stay ahead of changes as they come.
Contact us to speak to an industry expert about the future of your gas delivery and purification needs.
Share this Post: