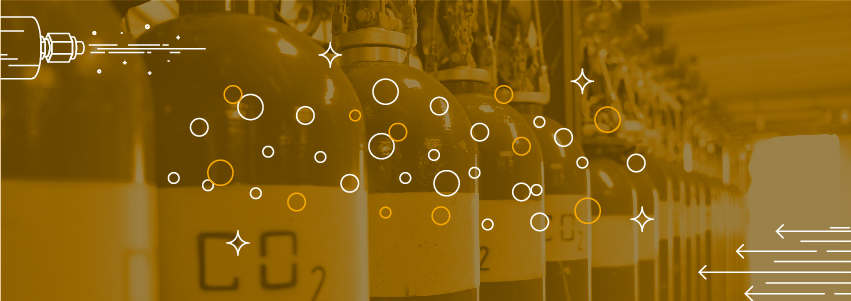
The Properties of Gas Purity: Gas Purification Media
From semiconductors and electronics, to clean energy and solar, industrial manufacturing, and universities, myriad industries rely on high or ultra high purity process gases to support their mission-critical work. In our first issue of our “Properties of Gas Purity” blog series, we covered three primary technologies leveraged for physical gas separation, each ranging in the level of purity achieved. In this, the second issue of our series, we will explore gas purification media, which vary in appropriateness depending on the specific impurity to be removed.
Let’s start with the basics. There are a number of materials, or media, that can be used within a gas purifier vessel to eliminate specific impurities. It is critical to note that a given media is both gas- and impurity-specific. The media that is leveraged to remove moisture, therefore, varies from that which is used to eliminate oxygen. Similarly, material used to eliminate oxygen varies from that which is used to eliminate nitrogen.
Many types of gas purification media can be highly reactive compared to media used in front-end gas separation. Activated nickel is one example: if even a percentage level amount of oxygen passes through this media, it can cause an exothermic reaction that could reach over 1000°C.
It is therefore vital to operator safety and process integrity that the right media is selected for the target impurity or impurities, and that strict safety protocols and controls are in place to properly utilize and store sensitive purification media. To help guide this selection process, we’ve compiled examples of common impurities and the most appropriate purification media to remove each of them:
The Impurity: Moisture
The Purification Media: Zeolites
In applications such as industrial manufacturing, where 5Ns of purity is required, the most common impurity to remove is moisture. In such cases, zeolites, which are readily hydrated and dehydrated, are ideal purification media. Working via physisorption, the physical bonding of gas molecules to a surface, moisture is removed from the gas as it flows through the zeolite.
However, it is critical to select the correct zeolite based on the gas utilized. While clinoptilolite, chabazite, mordenite, and erionite are all common zeolites utilized in gas purification, achieving optimal results requires that the properties of the selected zeolite align with the features of the gas. In cases where zeolites are not appropriately selected, saturated moisture can generate heat, improper pore size can negatively impact efficiency and capability, and incompatibility with corrosive and other gas classes can impact performance or compromise safety.
The Impurities: Oxygen & Carbon Monoxide
The Purification Media: Metal Catalyst
In cases where oxygen or carbon monoxide must be removed, a wide range of metal catalysts such as nickel, copper, and palladium are leveraged. These metals are often not utilized in their pure elemental form, but rather as high-surface-area powders residing on zeolites in quantities as low as 0.5 wt.%.
Removal of the targeted impurities relies on chemisorption, which forms strong electrical bonds between the surface and the adsorbate. Unlike physisorption, where Van der Walls forces create weak bonds between gas impurities and the surface, chemisorption leads to the creation of a distinct chemical species on the adsorbent surface. For example, if O or CO were to be removed from nickel, nickel oxide and nickel monoxide would be formed, respectively. Then, hydrogen is introduced at elevated temperatures, reacting with the catalyst to reduce the carbon and oxygen bonds and leave behind a pure nickel surface.
The Impurities: Methane & Nitrogen
The Purification Media: Rare-Earth Metal Alloy
The removal of methane and nitrogen requires the use of rare-earth metal alloys. Due to the highly reactive nature of rare-earth metals with impurities, these applications require even greater levels of diligence in order to prevent exothermic reactions with temperatures in excess of 2000°C from occurring.
In most cases where methane and nitrogen are removed, the purification media is zirconium-based. The alloy is then heated to temperatures above 300°C, at which point impurities are adsorbed onto the surface, becoming a permanent part of the alloy. Due to high temperatures and the reactive nature of the gases, operators working with rare-earth metals require purifier technology built specifically to operate at elevated temperatures.
Many Impurities. Many Media. One Gas Purification Partner.
In industries where gas purity is integral, ARM provides the Point-of-Use, Micro-Bulk, and Bulk purifiers needed for every application. Backed by our team of gas purification experts, our purification solutions uphold the most stringent standards for gas purity while also ensuring process safety. Explore our Product Finder to identify the right purifier by gas, product line, or industry.
Share this Post: