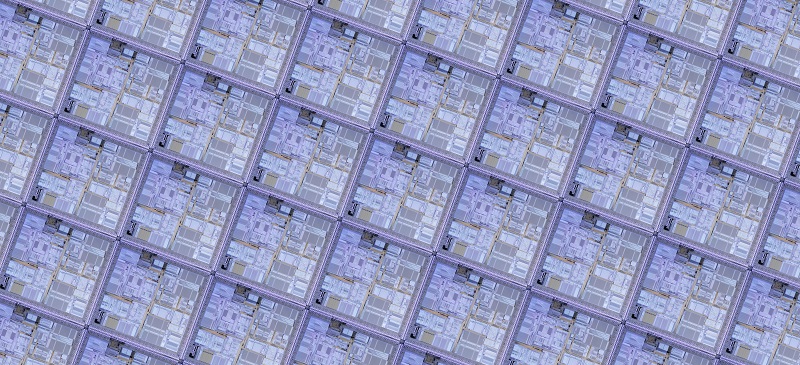
Six Steps to Successful Output: Gas Delivery’s Role in Semiconductor Creation
The electronics industry has advanced substantially from the first commercial transistors of the mid-twentieth century. Today, electronic systems have become increasingly complex, with the average computer chip comprised of over 10 billion individual transistors that take more than 1,000 steps to assemble into working components.
Still, at the heart of nearly all of these electronic devices are semiconductors, which are built and shaped using largely gas materials. In fact, gases have always been a key enabler of semiconductor fabrication, even though the types used continue to change and grow as manufacturing processes evolve. Gases have the ability to create chemical reactions at the molecular level, helping to shape a semiconductor’s electrical conducting properties to allow or prevent the movement of electrons. But, in order to ensure the semiconductor is configured to properly regulate electron movement, these gases must be precisely and accurately dispensed at every stage of its engineering process to incite the right reactions.
Understanding the processes used for semiconductor fabrication, and how gases are applied in each phase, provides insight into the important role gas delivery equipment plays in successful wafer creation. A recent article from Gasworld breaks down the overall semiconductor development process into 6 primary stages. Let’s review them, keeping in mind how an operator’s ability to precisely and accurately control gases in each stage can impact output:
Stage 1: Deposition
This is the process in which two-phase gas reactants are transferred into a metal-walled reactor, or chamber, while the semiconductor substrate is heated to a temperature that creates the desired reaction: the forming of a thin film product directly atop the previous layer. Temperature control is extremely important in this phase, and helium or other gases can be applied to help maintain appropriate temperature levels. This means the equipment used to dispense deposition gases must have high-performance control technology that enables precise management of gas flow rates and temperatures.
Stage 2: Photolithography
Once the substrate has been covered with the light-sensitive chemical film, a lithography tool, called a scanner, uses a laser light source to transfer an image onto the substrate, which is what will form the minute circuitry of the microchip. Wet chemical steps are then used to develop the pattern by removing portions of the chemical film.
An emerging form of photolithography uses excited tin vapor to create the light source, but requires large amounts of hydrogen to react with the tin and remove it as tin hydride so that it does not deposit on expensive optics. This is one example of the growing need for bulk gas delivery equipment to support increased gas volumes that new processes demand.
Stage 3: Etching
Etching is used to permanently realize the shape and pattern transferred during the photolithography process. Etchant gases are activated in the gas chamber, and then react with one material at the substrate surface preferentially to another. Most etchant gases are carbon-based and contain fluorine or other halogen atoms, and their composition helps determine the selectivity to their target film. Many of the gases used for etching are highly toxic, and so their gas handling systems must uphold stringent safety standards, such as those outlined in the SEMI S2 safety guidelines, to minimize operator risk.
Stage 4: Doping
Doping helps modify semiconductor conductivity, and involves adding atoms of semiconducting materials into a previously deposited semiconductor material to determine the exact conditions at which the semiconductor layer will conduct electrons. Gases used for doping include arsine (AsH3) and phosphine (PH3), which are both particularly toxic and therefore require storage in equipment that prevents leaks by limiting the effective pressure to lower than atmospheric. Diborane (B2H2) is also used in the doping process, but is a thermally unstable molecule that will slowly decompose. Gas mixing equipment can be leveraged to mix diborane with hydrogen to help control decomposition.
Stage 5: Annealing
Annealing is another process that can modify an existing thin film by initiating a reaction between a given layer with oxygen or hydrogen to create a new oxide or hydride layer. Such reactions typically take place at elevated pressures and temperatures. In order to create these reactions reliably and at the appropriate levels, equipment must again offer operators precise control over temperatures, pressures, and flow rates—allowing for high precision performance across annealing applications.
Stage 6: Chamber Cleaning
No less important than the stages that take place during the fabrication of a wafer are the steps taken to keep chambers in working order. While the bulk of excess chemical reactants are removed from the chamber during fabrication, small amounts can remain on chamber walls and equipment in the chamber even after the process has concluded. Impurities in concentrations as low as parts per billion have the ability to contaminate devices under fabrication, so chamber cleaning gases like nitrogen triflouride (NF3) are needed to properly purge the chamber of these particles between process steps.
In addition to the chamber itself, gas delivery equipment should also be purged during cylinder change-outs to maintain clean ultra high purity lines for the gases to flow through. Systems equipped with automatic system purging can assist in this decontamination process and help keep equipment always ready to start the next task.
It is obvious that gas materials are vital to semiconductor creation, but gas delivery systems are truly the lifeblood of these processes, as the way to deliver gases with tight control throughout fabrication. AES’ SEMI-GAS® systems have been helping semiconductor leaders power fabrication processes for over 35 years, and we will continue to evolve our equipment to safely and effectively handle the diverse gases needed to innovate electronics development today.
Share this Post: