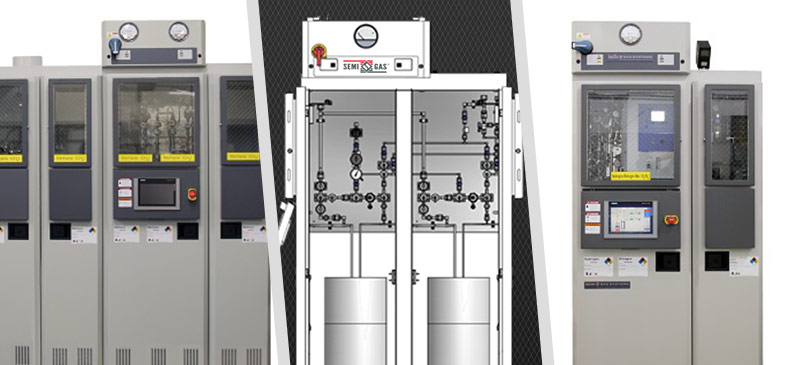
The View from the Front Lines: 3 Product Offerings That Were Directly Shaped By User Needs
In the world of high-tech innovation, no two process requirements are alike; the demands of the gas delivery systems used to support these applications are equally diverse. From various standards for control technology, to gas purity, system configurability, and more, manufacturers and researchers have a myriad of factors to consider to select the right gas source and distribution equipment for their needs.
Oftentimes they have rigorous and highly specialized requirements that standard gas delivery systems simply cannot meet. These off-the-shelf solutions are either too rigid or feature-restricted, and the time and cost to customize them for the specific functionality needed – if they are able to be modified at all – expands scope quickly and keeps operators waiting, leaving valuable innovation time on the table.
But what if you had a systems partner that shaped their equipment from the start with customers’ diverse and increasingly complex requirements in mind, and designed their solutions from a customer-first perspective? This leads to more versatile gas delivery equipment that can be easily optimized for a wide range of specific applications. Let’s explore three instances where AES’s gas delivery innovation stemmed directly from customer-driven requirements.
EXAMPLE 1:
On-Site Gas Blending for Diverse Applications
Typically, operators whose processes require forming gas mixtures must purchase expensive pre-mixed cylinders. However, there is often a need for more than one mixture or the operator needs the ability to vary the blended ratios. Seeing firsthand the inflexible options one of its customers had, AES set out to develop a gas mixing blender that would allow the operator to mix their own formulations to the exact ratios required, on-site in their own facility.
The SEMI-GAS® Xturion™ Blixer™ was born from this customer’s specific demands for precise gas mixing for their high-volume application, and eliminated their need to stock a variety of pre-mixed forming gas concentrations while also decreasing the frequency of cylinder change-outs and tool downtime. But AES also developed the Blixer with other gas blending applications in mind, and ensured it was built from the ground up with the flexibility to be easily pivoted for use in other like processes.
As a result, the Xturion™ Blixer™ has become a staple system in the process environments of many AES customers across high-tech industries—ranging from laser-based technology development to semiconductor fabrication, electrically-powered vehicle manufacturing, and sustainable energy solutions—and gives each operator using it the precise, real-time control they need to custom-blend gas mixtures in the exact ratios they require.
EXAMPLE 2:
Bulk Specialty Equipment Customized for Unique Chemical Coating Process
When a leading global tooling provider requested a specialized bulk gas delivery solution to support its chemical vapor deposition (CVD) processes, AES knew its SEMI-GAS® Megaturion™ MegaCyl Bulk Specialty Gas System would provide a versatile base solution to easily adapt to the company’s demands.
The standard Megaturion™ MegaCyl systems are designed for high flow gas applications requiring automatic switchover of two or more process cylinders, but also have the ability to be flexibly configured as multi-cylinder gas cabinets or rack mount systems, and can safely support a variety of hazardous process gases. By building up from the MegaCyl’s inherent flexibility and adding key custom functionality specific for CVD processes, AES was able to decrease both the system manufacturing turnaround time and cost compared to a fully custom equipment solution.
EXAMPLE 3:
Standardizing Custom Functionality for Liquid Delivery
Upon first releasing the original custom SEMI-GAS® Xturion LPX™ (Liquid Push System) design, AES received numerous requests from customers asking to have the system further tailored to their own process needs. After multiple additional custom design iterations, AES was armed with the in-field knowledge needed to create a single, standardized model of the LPX™ that encompassed the most sought-after safety and performance features requested by operators for optimal liquid delivery.
While the standardized model can be used for a diverse range of liquid delivery applications, it is also a flexible platform onto which additional functionality can be easily added. For example, AES recently equipped the LPX™ to support the supply of tetraethoxysilane (TEOS) liquid source material for a customer’s specific ultra high purity application. Through minor adjustments to the standardized system, AES was able to extend the LPX’s usefulness for the customer without developing a net-new, fully custom solution. Not only did this modification meet the customer’s requirements, but it also now enables other operators to leverage the LPX platform for their TEOS handling needs.
Shaping Gas Delivery Systems Around the Customer
At AES, we recognize that optimizing systems for our customers starts with designing systems with a customer-first mindset. That means not only listening to customers’ requirements and challenges, but also working with our team of industry experts to construct diverse, extensible solutions to solve real operators’ real problems.
Want a gas delivery partner whose systems are built with your challenges in mind? Contact AES to get started today.
Share this Post: